Introduction
Welcome to our latest newsletter on SAP Profitability and Performance Management (PaPM) and its innovative approach to cost allocation. In this edition, we delve into the dynamic structure for cost allocation in PaPM, exploring its capabilities with a business case.
What is cost allocation?
One of the most common use cases of PaPM is Cost Allocation. Although it depends on the business process, there are many methods of making cost allocations. SAP Controlling module offers options as standard functionality within the system for plan and actual allocations. PaPM offers a much more flexible and high-performance solution with more functionalities. PaPM also has ability to combine data from different systems (SAP or Non-SAP), enrich your existing data and send the results to different systems.
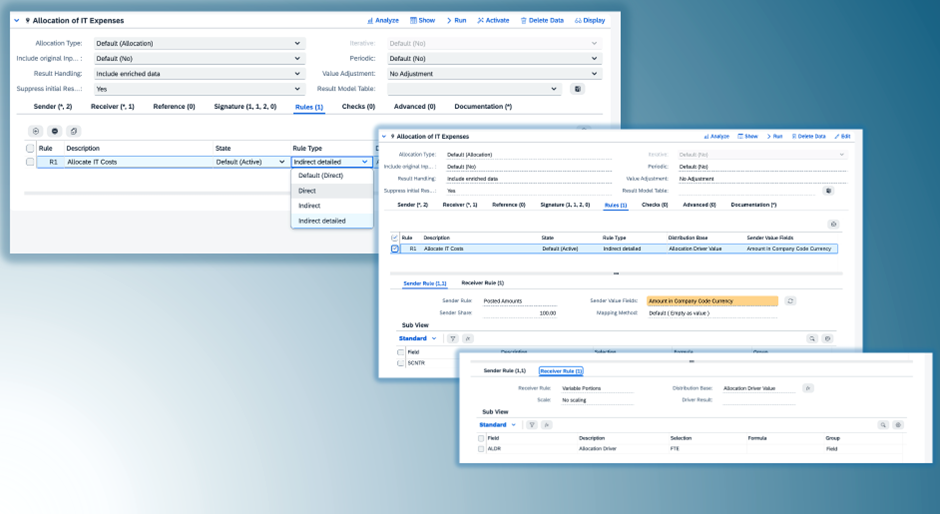
The cost allocation cycle rules are one of the most detailed processes to be implemented in a system because Cost allocations might have many allocation rules which define the restriction of allocation sender and receiver dimensions. Most of the clients have many allocations and hundreds of segments due to the financial reporting requirements of the company. You can define as many as allocation rules in PaPM from scratch or you can retrieve existing allocation rules from a system, and you can use them in your reporting. Especially, when comparing plan and actual results based on the same allocation rules which are currently used in your system. The ability to retrieve tables in the existing system allows you to use SAP allocation cycle configurations for another data set like planning or budgeting in PAPM without configuring them from scratch.
Business case: You have SAP analytic Planning tools for your annual planning processes and to reach the outcome of planning you need to allocate OPEX and CAPEX based on Actual allocations which provide a basis for reporting to compare the plan and actual results.
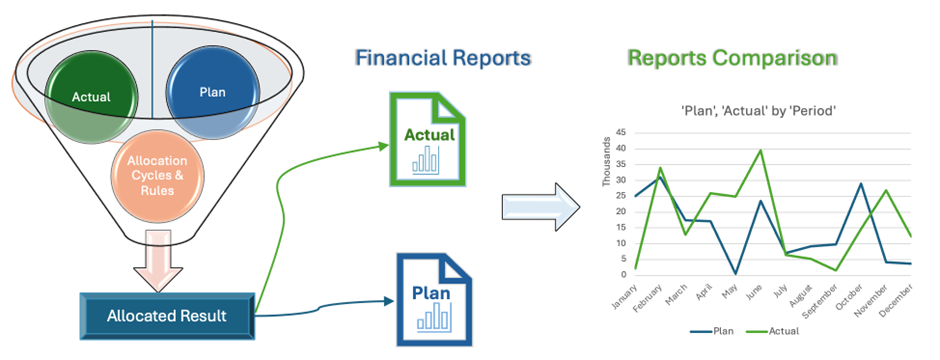
Solution: Behalf of the business process you can use the actual cycle to allocate planned cost with fetching plan data from SAC or BPC platforms. PaPM provides you with various options to build your technical structure. One of them is to combine Actual system configuration and Plan data of the Planning tools.Solution: Behalf of the business process you can use the actual cycle to allocate planned cost with fetching plan data from SAC or BPC platforms. PaPM provides you with various options to build your technical structure. One of them is to combine Actual system configuration and Plan data of the Planning tools.
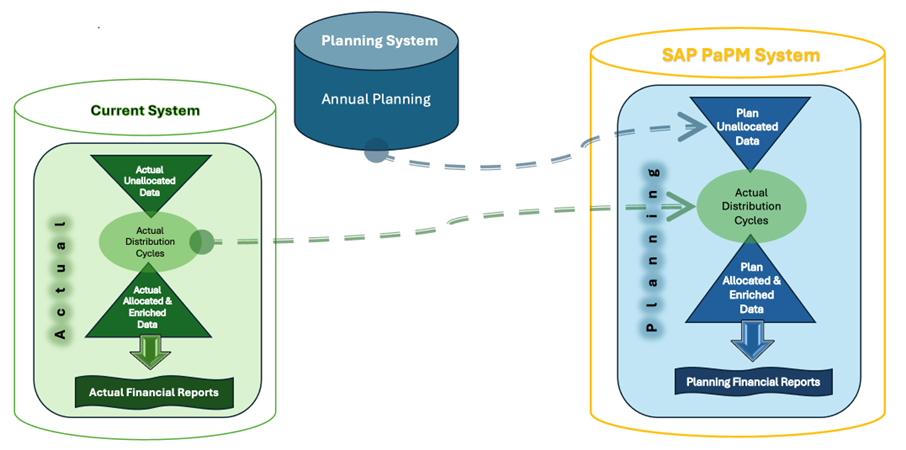
Real-time reports are based on actual financial data and actual allocations in the actual system. These actual allocations can be used to distribute expenses in annual planning data. The outcome of this approach is to allocate actual and plan data on the same basis. This means that results can be compared on an apples-to-apples basis. To do this we need to reach out configuration of the actual allocation cycles via SAP tables which contain details of the cycles, such as T811K, T811S, T811D etc. These tables have all the information what needed for an allocation, sender/receiver cost centre, cost element or groups. Besides this SETHEADER and SETLEAF tables also need to be retrieved for master data of the groups. After retrieving the master data and the cycle configuration table you can enrich these tables with Join or View functions in PaPM for split the sender and receiver input functions of allocation. You can build a dynamic allocation structure based on these tables in PAPM. This eliminates the need to update cycles or master data as they are automatically updated from the tables.
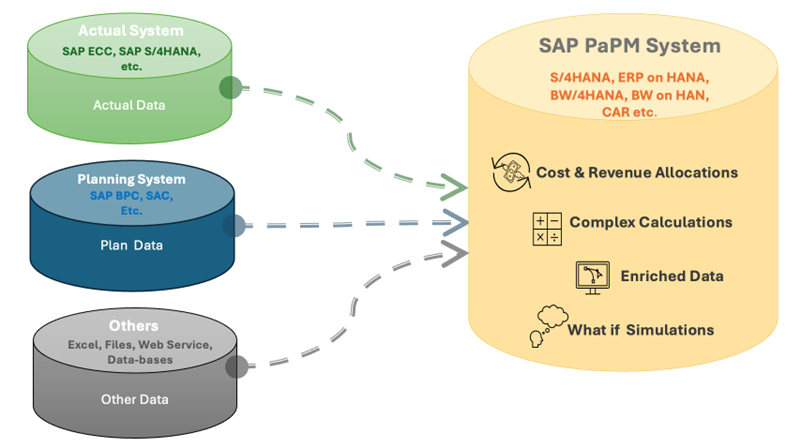
Conclusion
This approach provides you,
- Dynamic structural usage, especially for the planning processes in global companies.
- Central process management and comparison of apples-to-apples.
- No need to update plan cycles manually and that saves time. They will be automatically updated from the actual cycles or master data if any changes happen.